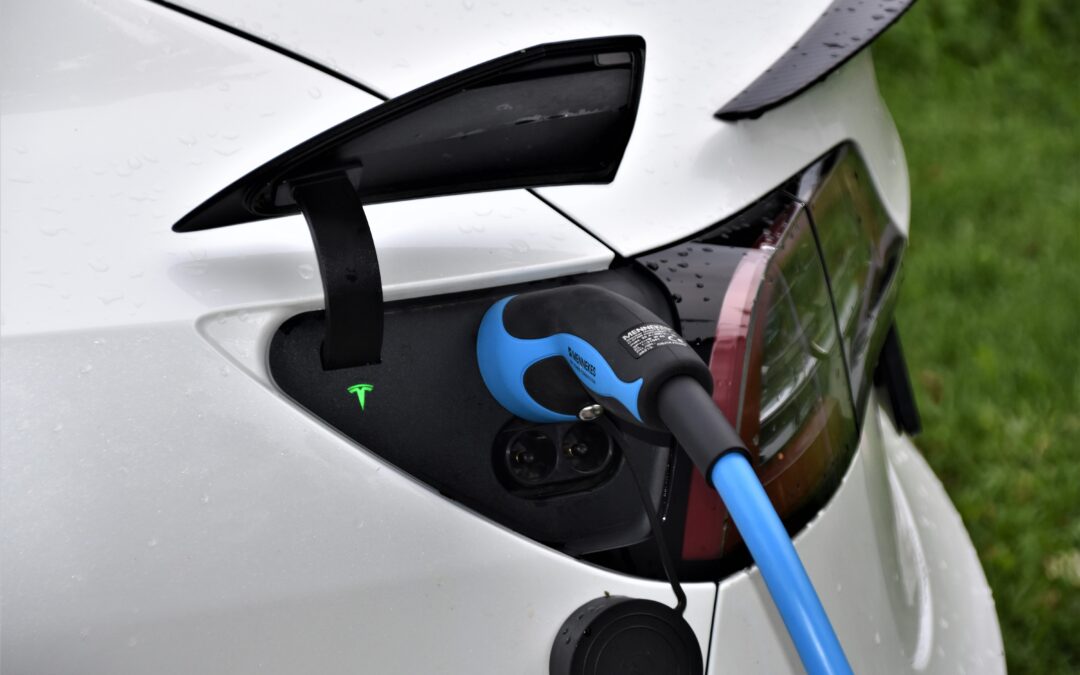
Getting Specific About Effective Energy: The Truth About Comparing Batteries
Don't be mislead: apples-to-apples battery measurement
In the race for dominance in the energy storage market, battery manufacturers like to brag about a battery’s specific energy: how many watt-hours are delivered by each kilogram. But is it the right way to compare battery technologies? In short: no. It glosses over some critical real-world issues and results in misleading comparisons.
To use a very simple analogy, imagine you want to ship a gift to a friend. You have the choice between a selection of cheeses or a book. They both weigh the same and are about the same volume, and they should cost the same to ship, right? Wrong. While the weight and volume of the gift is the same, the effective weight and volume of the shipped package won’t be, and neither will the cost. One requires icepacks and a cooler to arrive fresh while the other can simply be put in a box. To make a meaningful comparison, you need to compare the whole package.
And it’s the same with battery systems. Comparing the innermost component of the system—a cell—does not result in an accurate comparison.
Cells make up modules which make up packs. And that’s not all; we must consider the whole battery system. For electric cars for example, the lithium-ion battery system also needs the Battery Management System (BMS), the active cooling system or Thermal Protection System (TPS), and protective armor. Each system adds weight, volume, and cost.
Why are these three measures important? The two most looked at numbers are specific energy in Wh/kg (watt-hours per kilogram) and energy cost in $/kWh (dollars per kilowatt-hour). The first tells you how much energy you can store for a given weight. The second tells you how much this energy costs you. In applications where space is limited, a third measure, energy density measured in Wh/l (watt-hours per liter) can also be essential. They are a way to compare battery chemistries and battery system designs.
Specific energy vs. effective specific energy
Typically, articles about batteries focus on the specific energy of just the cell, the innermost component of the battery system. The numbers can look good: after all, it is light without its supporting systems and relatively inexpensive. But what’s more revealing is the effective specific energy: how the whole system measures up.
It is fair for cell manufacturers to simply compare the cell, the smallest component in the battery, because they do not know how the cell will be used. But as soon as you know how a battery will be used, there’s other important information to consider. For example, the battery for an electric bike is small in capacity (Wh), does not need a sophisticated BMS, just uses air to cool it, and doesn’t need much armor to protect it.
Next time you hear an analyst predict an aggressive target price for lithium-ion batteries or an entrepreneur pitch a new battery chemistry, raise the discussion up to the whole system level.
However, a passenger electric vehicle, which weighs more than an e-bike, carries more people, and travels much faster and further. So it requires a much higher capacity battery pack, an active cooling system moving a cooling fluid through channels to cool the cells (since it gets hot moving and accelerating), a sophisticated BMS with computer, sensors, and cabling, and armor to protect the installation in case of a crash which could penetrate the pack and set the pack on fire. These three main subsystems add weight, volume, and cost.
For specific energy, increasing the weight (kg) decreases specific energy. For energy cost, increasing the dollars obviously makes it go up. And for energy density, increasing the volume lowers the energy density. In other words, while the cells still supply the same Watt hours, the battery system installed in an EV is effectively heavier, more expensive, and bulkier per unit of energy than the battery system installed in an e-bike.
When comparing different battery chemistries, the comparison should be at the system level. The discussion needs to be about the effective (or installed) specific energy, energy cost and energy density so it’s an apples-to-apples comparison.
One car, two ways to look at its battery
Let’s take a real-world example. The Chevy Bolt uses LG NMC cells with a specific energy of around 220 Wh/kg and a cell cost of $145/kWh. After all the pack level hardware and protective subsystems are accounted for the installed specific energy drops to 135Wh/kg and the installed cost rises to $225/kWh.
The numbers look even worse when the current recall of all Chevy Bolts due to fire risk is taken into account. Because every battery pack is being changed out, one could say the effective energy cost is really $370/kWh.
Changing the size and the chemistry of the battery pack can make a significant difference. For example, if the Bolt had a lower range vehicle for use in an urban setting, say 40kWh pack with a 200 mile range (after all, 95 percent of trips are under 30 miles), it could use a different type of lithium battery, lithium ferrous phosphate (LFP), or a nickel zinc (NiZn) battery. Both have a cell specific energy of 130Wh/kg and a cell cost of $100/kWh. And because they are both less prone to fires, they do not need a sophisticated BMS, no TPS and no armor.
This means that the installed specific energy would be 115 Wh/kg and a cost of $160/kWh. Why only 200 miles? That’s where energy density comes in: both of those chemistries have a lower energy density than lithium ion, so only a lower range battery pack will fit in the space in the Bolt and not change the weight significantly.
Looking beyond battery marketing
It’s popular to think that lithium-ion batteries have already won the race to dominate most energy storage markets, and much of the argument is centered on its competitive specific energy and cost. But with a true comparison of the effective or installed specific energy and cost, it’s clear that it’s not the natural winner for many use cases.
Next time you hear an analyst predict an aggressive target price for lithium-ion batteries or an entrepreneur pitch a new battery chemistry, raise the discussion up to the whole system level. How do the numbers look once you have accounted for the full system for the energy use case, whether it’s an e-bike, EV or grid storage? The first answer might not be the most relevant answer for the economics. Or for the environment which is the subject of another article.
Image: Photo by Waldemar Brandt on Unsplash