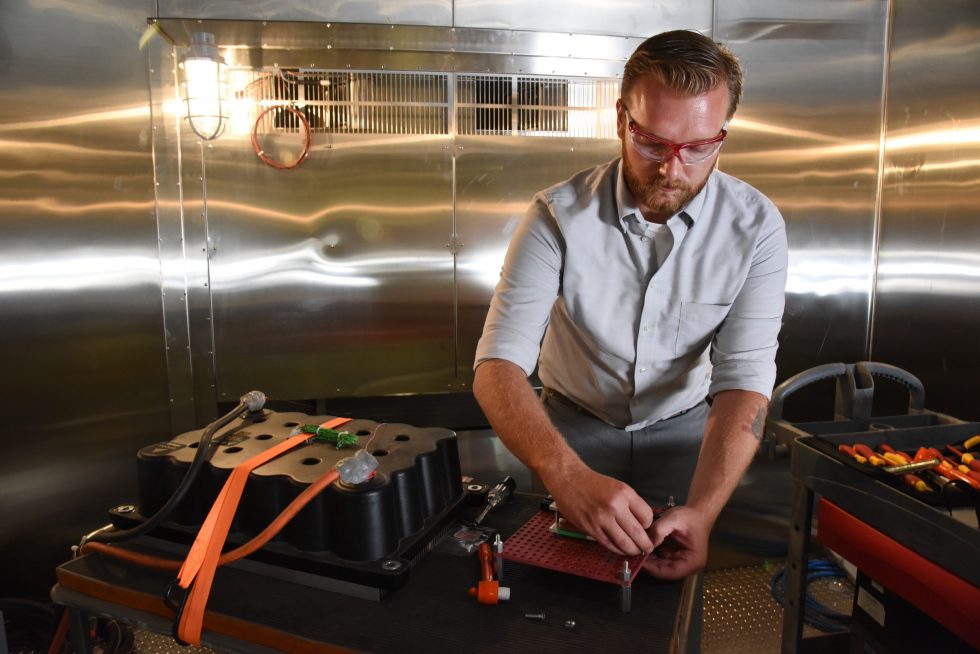
Scaling Energy Storage Manufacturing is Essential for U.S. Energy Independence
Energy Independence Day, Part II
For the United States to get even close to energy independence it needs to invest not only in traditional energy infrastructure—especially the electric grid—but also in the new technologies to enable that infrastructure. And the most important piece of that more broadly-defined infrastructure is, arguably, energy storage.
Why? Even if the clean energy provisions that were pushed out of the infrastructure bill are revivified in a reconciliation bill, the United States cannot meet its clean energy goals without moving rapidly to electrify (almost) everything and doing that requires massively scaling energy storage.
Just as investment in the grid’s transmission is essential to move energy from where it is produced to where it is needed, investment in energy storage is essential to move energy from when it was produced to when it is needed.
This goes both for short-term energy storage—moving energy produced by wind mainly at night or by solar in the height of the day to the early evening peak—and long-term energy storage—moving summer’s excess solar production to the middle of the winter when days are shorter, and panels may be buried by snow. It also applies to energy needed for mobility: EVs, electric buses and urban electric vehicles and electric micro mobility are all part of electrifying everything.
Aiming for energy independence
Energy independence involves having some control over the materials in energy storage, as explored in our recent blog U.S. Energy Independence Depends on a Smart Supply Chain Strategy. But it also involves having some control over energy storage manufacturing.
Most people don’t think about infrastructure until it fails. When it’s headline news—a pipeline shut down by hackers leading to gasoline shortages, abnormally cold weather resulting in a massive grid failure, extreme fire danger prompting preemptive power shutdowns—infrastructure’s essential role is brought into the spotlight. However, the time to think about infrastructure is before you need it, because planning and building infrastructure takes time. The same is true of the means of production for infrastructure.
Just as investment in the grid’s transmission is essential to move energy from where it is produced to where it is needed, investment in energy storage is essential to move energy from when it was produced to when it is needed.
Like mining and refining energy storage materials, manufacturing energy storage is largely done in other countries. If the U.S. wants better control of the supply chain, that has to change.
Time is not on our side. It will take decades to create lithium battery infrastructure, both materials and manufacturing plants.
Innovation in energy storage manufacturing
The good news is there is a way to leapfrog the conventional path of mining lithium battery materials, setting up plants to refine the material and building new Gigafactories.
The U.S. can meet this urgent need with an innovative approach. We already have significant manufacturing capability and capacity when it comes to lead acid batteries. The U.S. can take advantage of that energy storage manufacturing by converting existing lead acid plants and NiMH/NiCad plants to make advanced zinc-based batteries. Taking those factories’ output capacity in terms of specific energy, this effectively doubles or triples their energy storage manufacturing capacity.
We need to think outside the lithium-ion box if we are to move towards energy independence. By taking advantage of our existing leadership in lead-acid manufacturing plants we can make them Gigafactories in two years instead of ten, catapulting the U.S. into advanced battery manufacturing far sooner and with a lower capital investment while retaining and expanding American jobs.
Image: Idaho National Laboratory’s Battery Test Center includes test chambers for batteries of all shapes and sizes.